Contents
Brainboxes explains the basics of Industry 4 and how to create a smart factory in five easy steps
The aim of Industry 4 is to create a smart factory, combining the intelligence offered by IT systems with automation.
In the smart factory the physical machinery of the factory floor is connected to your computer network, the Internet or a Cloud Service. This enables you to monitor and control all your machines from a central PC, tablet or smartphone, either locally or remotely.
By controlling your machines at one central point, you can streamline your factory floor and increase automation in your workplace. Just as importantly, as you monitor the machine data fed to your computer network, you can use a variety of software packages to gain valuable intelligence and insight into your processes and discover new ways to increase efficiency and productivity. When a company embraces Industry 4, there are often substantial financial benefits.
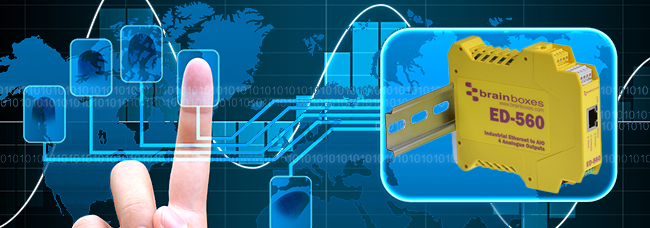
Industry 4 and IoT
Reports agree that industry will account for a large proportion of the devices connected in the Internet of Things (IoT). (Note that Industry 4 and IoT are two terms which essentially describe the same concept.)
There is no reason to delay; the technology exists today to make Industry 4 a reality.
Since production machinery often represents one of the largest capital investments for businesses, updating production lines can be prohibitively expensive and it is often a major strategic decision. However, purchasing brand new equipment just to get an ethernet port is a costly enterprise, and that’s where Brainboxes comes in.
We are one of the few connectivity specialists to manufacture universal control and monitoring devices which can be ‘retrofitted’ to equipment of all ages. This means you can exploit the significant benefits and advantages of Industry 4 without updating your equipment by installing a Brainboxes product that connects you to the wealth of information trapped in your machines.
Remote I/O devices provide a way to make that IoT connection and take the first step towards Industry 4. Brainboxes manufactures a range of devices in the UK that connect to just about any machine so you can transfer data and information to your IT network or a Cloud Service.
Although we focus on factories and production lines in this article, Brainboxes’ technology has a wide range of applications:
- It can be used in facilities management or residential buildings to monitor and control energy usage, entry systems, lighting, heating, ventilation and air conditioning equipment.
- It can be used in site security to monitor and control CCTV cameras, smoke detectors, proximity sensors, automatic lights, alarms, proximity sensors and automatic entry barriers.
- It can be applied to retail point of sale to connect barcode scanners, credit card readers and cash drawers.
- It can be utilised in distribution centres to track products coming in and out of sites and buildings.
- It can be applied to material handling operations to develop unmanned forklift truck systems with onboard proximity sensors.
- It can be used to track machine usage and uptimes to enable more efficient predictive maintenance routines.
Whatever your machine or device, wherever it is, there is a Brainboxes control and monitoring option that will work for you.
The journey to Industry 4
Here is the way Brainboxes pictures the journey from the machine level to Industry 4 insight and beyond:
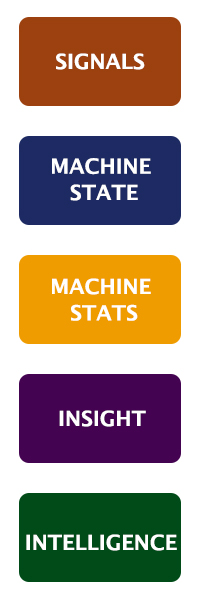
-
Machine signals
Machines produce signals just by being on. A basic example is a light that indicates when a machine has power. Inside a machine there will be signals that turn on fans in response to temperature, or change the colour of the Andon light if the conveyor stops. Outside the machine there are also signals produced by common sensors. Lots can be measured by a simple two wire sensor and this provides a very affordable way to add monitoring to a machine.
At this level these signals can be pretty rough, noise really, that doesn’t mean much by itself, such as high/low, on/off, 1/0. But, this is all the input needed for a remote I/O device. These signals can be taken from the machine, from a PLC, HMI or from stand-alone/add-on sensors.
-
Machine state
When we assign a value to signals they start to become useful to us. For example, if the signal to the fan is high (it is on), coupled with the conveyor running then the machine is ready to build. The machine is in a good state so the Andon light is green. If the light is green and a sensor detects an object then we can say a product has been built.
-
Machine statistics
By recording the machine state over time we can start to determine how much of a production shift a machine was up and running for, or how long it took complete a cycle and make a product. This is the basic data needed to complete the OEE equation. This requires data to be stored in a database, which can either be on a sever, in the cloud or by the device itself in what is known as edge processing.
-
Insights
Essentially machine statistics over time; insight can be achieved by looking at patterns in shift data. Like correlating machine temperature against breakdowns or optimising the maintenance schedule.
This is where we reach a level of abstraction, a step away from the factory floor and the mechanical processes, where we add in the factors and nuances that are unique to our application. The insights and resulting changes can be surprising and extend beyond the production line.
-
Intelligence
The last level is to use intelligent software to learn machine patterns, increase productivity and implement predictive maintenance. There are easy-to-use platforms and software out there already that aim to help with this: Node-RED visual flow software, IBM’s Watson, Google’s Cloud Prediction API and TensorFlow, and Microsoft Azure. All offer Cloud-based ways to tackle data analytics, whether it’s big data or just big to you.
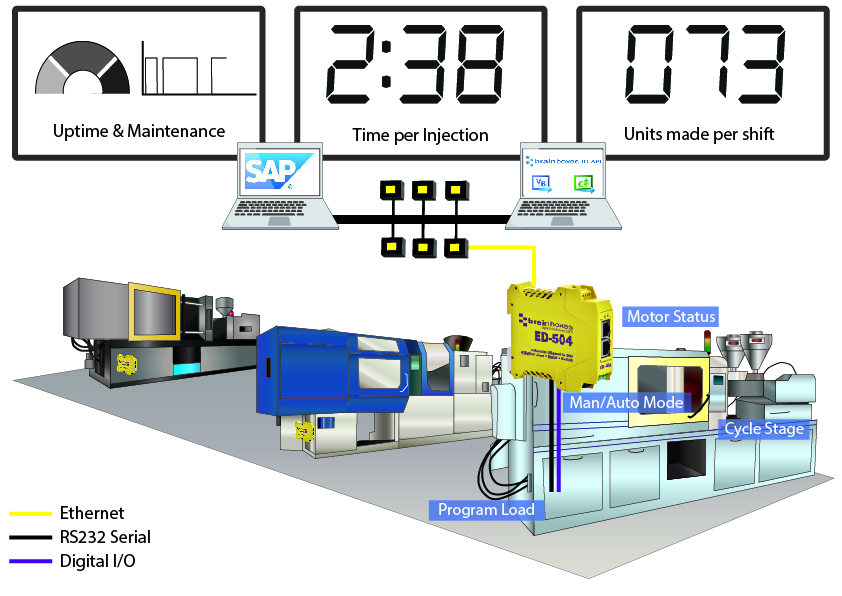
Start your journey with Brainboxes
We offer reliable digital and analogue devices that are compatible with hardware and software, enabling you to take a firm step on your industry 4 journey, no matter where it leads.
Our support teams are always on-hand to help you explore and discuss this technology and how it could be applied to your business. If you have any questions, please feel free to get in touch with our customer support team via email at [email protected] or over the phone on +44 (0) 151 220 2500. We look forward to hearing from you. To find out more, below are just some of the connectivity devices that we manufacture in the UK and sell in more than 40 countries worldwide.
-
BB-400 Neuron Edge Industrial Controller
- Powered by an industrialised Raspberry Pi and Arduino
- Multiple connections
- Includes easy-to-use secure web interface
-
Remote Digital IO
- 8 Inputs and 8 Outputs
- Easy to use with API support
- Industrial Specification and format
-
Remote Analog IO
- 8 Analog Inputs
- Simple Installation
- Great for flow and pressure monitoring